Baling wire is a fundamental tool in various industries, from agriculture to recycling. Despite its simplicity, choosing the right type of baling wire can significantly impact operational efficiency and cost-effectiveness. In this article, we delve into the intricacies of baling wire costs, backed by expert insights and firsthand experiences, to help businesses make informed decisions.
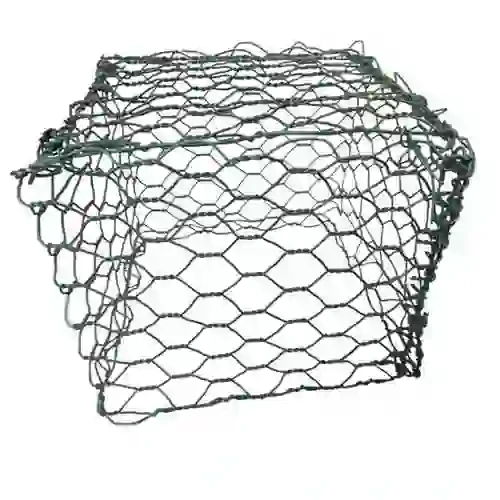
Understanding the cost of baling wire involves more than its initial purchase price. Various factors must be considered, including material type, tensile strength, and application requirements. High-carbon steel wire, for instance, offers excellent strength and is often used for compacting heavy materials like cardboard and plastics. However, it is typically more expensive than its low-carbon counterpart. On the other hand, galvanized steel baling wire, favored for its rust resistance, might be slightly more costly but offers long-term savings by preventing corrosion.
A seasoned expert in the recycling industry shared a valuable insight Investing in the right baling wire pays off in the long run. We switched to a higher quality wire and noticed a significant reduction in machine downtime and binding failures. This highlights the importance of assessing the total cost of ownership rather than merely focusing on upfront expenses.
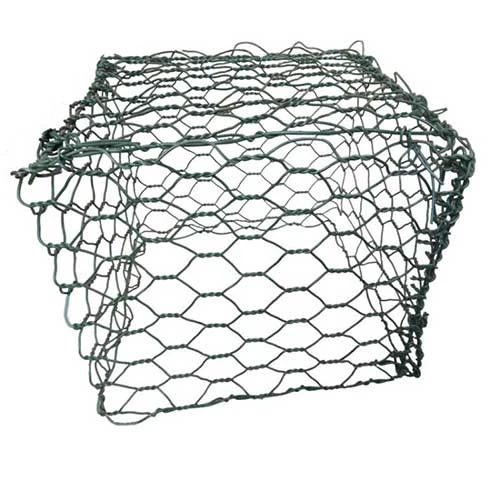
Operational efficiency is another crucial consideration. Baling wires that are prone to snapping can halt production lines, leading to increased labor costs and delayed shipments. Many businesses have found success by consulting with specialized suppliers who provide tailored advice on the most suitable wire for specific applications. Such collaboration not only enhances performance but can also result in bulk purchasing discounts, effectively reducing the effective cost per unit.
Furthermore, the environmental aspect is gaining prominence. A move towards sustainability has encouraged the use of biodegradable baling twine as a substitute for traditional wires in some sectors. While initially pricier, they can reduce landfill waste fees and meet governmental regulations, offering potential financial benefits.
baling wire cost
Experts also advocate for regular training of personnel handling baling operations. Proper handling not only extends the lifespan of the wire but also ensures safety and minimizes waste. Companies have reported up to a 20% reduction in costs by investing in comprehensive staff training programs. Such investments affirm an organization's commitment to safety and efficiency, thereby enhancing trustworthiness with stakeholders.
Trust in suppliers cannot be overstated. Businesses should establish relationships with reputable vendors that offer transparent pricing, detailed product specifications, and excellent customer support. Many leaders in the packaging industry emphasize this approach, recounting experiences where they secured better deals and reliable service through long-term supplier relationships.
An authoritative voice in manufacturing shared their strategy We conduct annual audits of our suppliers. This ensures that they adhere to quality standards and allows us to negotiate better contractual terms, which directly impacts our overall production costs.
When talking about the cost, shipping also plays a role. Bulk purchasing might offer per-unit savings but necessitates sufficient storage space and logistic facilities. Companies must weigh savings against the potential costs of warehousing, possibly utilizing a just-in-time inventory system to maintain balance.
In conclusion,
the cost of baling wire goes beyond the sticker price. Businesses need to evaluate their specific needs, operational dynamics, and long-term financial implications. By focusing on quality, sustainability, and supplier relations, companies can optimize their baling wire investments, resulting in enhanced productivity and reduced overall expenses.