Baling wire is an essential component in various industries, playing a crucial role in packaging, agriculture, and recycling. When delving into the specifics of baling wire gauge, understanding its significance can greatly enhance operational efficiency and product effectiveness. This article explores the intricacies of baling wire gauge, providing insights to aid in selecting the most appropriate gauge for specific applications.
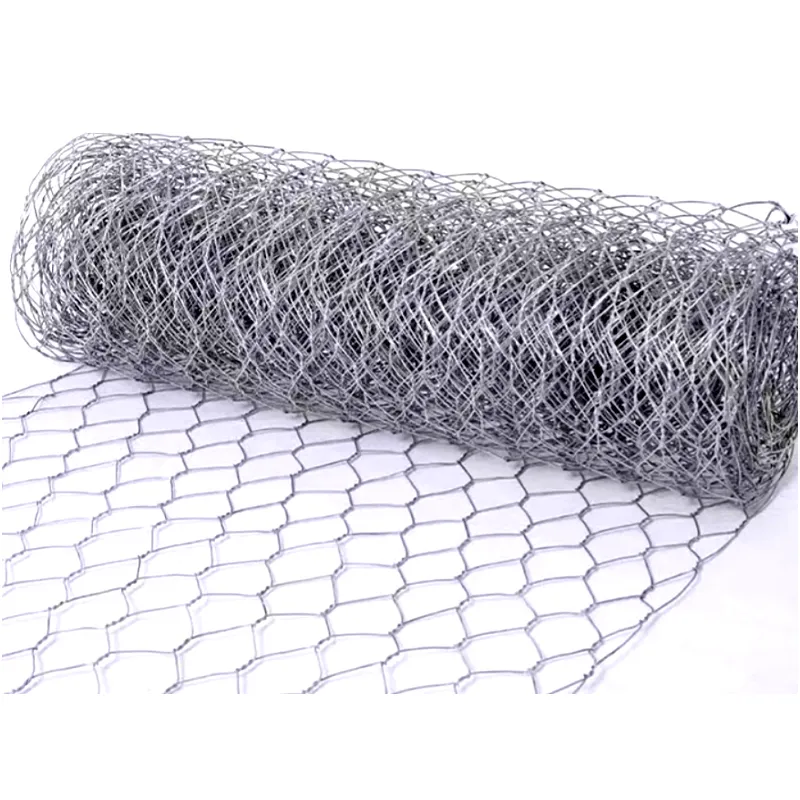
Baling wire gauge refers to the thickness of the wire, which is a critical factor determining its strength and flexibility. The gauge system, predominantly used in the United States, indicates that the lower the number, the thicker the wire. Knowing this can be vital for choosing the right wire gauge, as different materials and bales have varied requirements for securing and holding.
In agricultural settings, for instance, baling wire is often used to bundle hay. A thicker wire, typically a lower gauge such as 11 gauge, is preferable for heavy or dense bales to ensure durability and reduce the risk of breakage. This level of thickness provides the necessary tensile strength to withstand the pressures of handling and transport without compromising security.
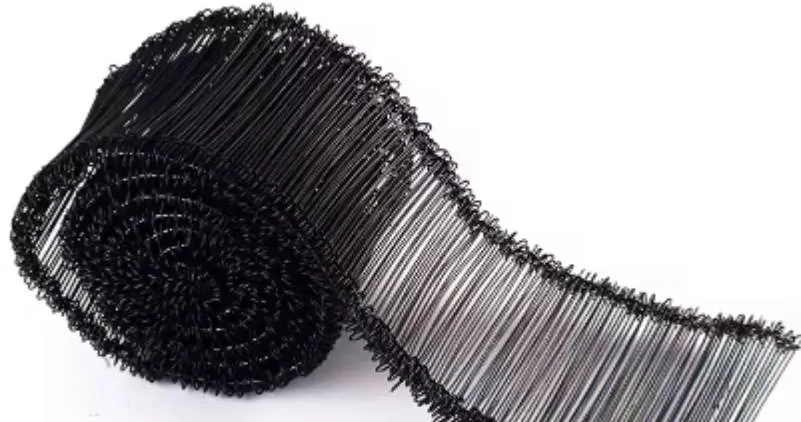
For recycling applications, thinner wire gauges, such as 14 or 16, may be adequate, depending on the material being baled. These wires are generally used for materials that aren't as dense, like cardboard or paper products. Utilizing the correct gauge wire for these lighter materials helps in maintaining not just the integrity of the bale, but also in optimizing costs associated with wire usage.
Professional balers and packaging specialists recognize the significance of selecting the right gauge. A deep dive into industry standards reveals that choosing the correct gauge can prevent losses in product, manpower, and resources. In scenarios where high volumes of bales are handled daily, such as recycling plants or large-scale farms, the financial implication of using a poorly chosen baling wire gauge could be substantial.
baling wire gauge
In addition to understanding the gauge system, professionals rely on their hands-on experience to make informed decisions. For instance, feeling the wire for flexibility, testing it against load weights, and assessing its performance in securing bales under varying environmental conditions are all part of the real-world scenarios that influence decision-making.
However, expertise also comes from knowledge rooted in scientific and engineering domains. Engineers involved in the manufacturing of baling wire pay close attention to properties such as tensile strength, elasticity, and corrosion resistance. Their expertise ensures that the wire not only meets industry regulations but also surpasses the expectations of durability and performance. This informed approach builds trust with consumers, who rely on the manufacturer's reputation for delivering high-quality, long-lasting products.
Trustworthiness, a crucial component in the selection process, is often established through transparent business practices and a commitment to quality assurance. Companies that provide extensive product testing results, clearly defined specifications, and customer support channels instill confidence in their offerings. For users seeking guidance, these avenues offer a wealth of information, including insights into wire composition, coating options for rust resistance, and best practices for application.
Authoritative voices in the industry, such as seasoned agricultural professionals or recycling specialists, often share their expertise and experiences through forums, trade shows, and publications. These exchanges further enrich the collective understanding of baling wire gauge, contributing to a body of knowledge that is both theoretical and practical.
Ultimately, choosing the right baling wire gauge requires a balance of experience, technical knowledge, and industry trust. By combining these elements, users can ensure that their selection not only meets the immediate needs of the task but also adheres to broader operational goals of safety, efficiency, and cost-effectiveness. As industries continue to evolve, ongoing education about advancements in wire technology and application techniques remains imperative for optimizing the value of baling wire across various sectors.