Baling wire gauge, a seemingly mundane aspect of the baling process, plays a crucial role in ensuring efficiency and reliability in various industrial applications. Despite its apparent simplicity, selecting the correct gauge is an art rooted in engineering principles and practical experience. This guide delves into the nuanced dimensions of baling wire gauge selection, providing insights that both seasoned professionals and newcomers will find invaluable.
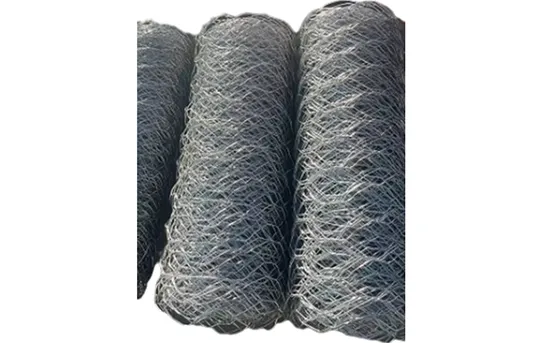
In the realm of agricultural and industrial baling,
choosing the right wire gauge is paramount. The gauge, essentially the thickness of the wire, dictates its strength, flexibility, and suitability for different materials. A wire that’s too thin may snap under pressure, while a wire that's too thick can be unnecessarily costly and cumbersome to work with.
Material is the first component to consider. Baling materials vary widely, from soft textiles and paper to dense hay and cardboard. For lighter materials, such as clothing or paper, a higher gauge wire, which is thinner, is typically sufficient. Conversely, tougher materials like hay bales or large cardboard stacks necessitate a lower gauge, thicker wire that offers greater tensile strength.
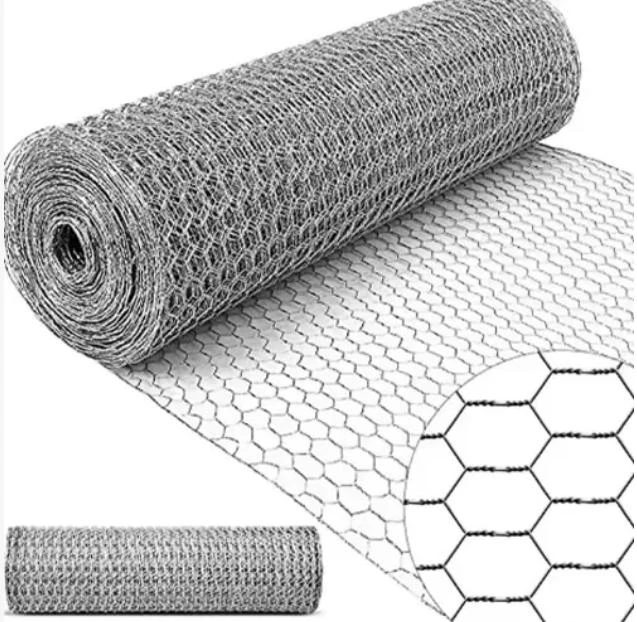
Durability is influenced by the material's environment. If bales are stored or transported in areas prone to humidity or chemical exposure, galvanized or coated wires offer additional protection against rust and corrosion. This protective layer ensures longevity and reliability even in challenging conditions, safeguarding the integrity of the bale and minimizing material loss or damage.
Cost-efficiency comes next. While lower gauge, thicker wires offer higher durability, they are often more expensive. Balancers are therefore faced with the challenge of finding a middle ground where cost does not compromise durability or utility. The aim is to optimize the gauge selection ensuring that it not only supports the bale securely but also aligns with budgetary constraints.
Understanding the mechanical properties of wire is vital. Wire tensile strength, elasticity, and bend resistance are critical factors influencing gauge choice. Tensile strength measures the wire's ability to withstand tension without breaking. Elasticity determines the wire's capacity to stretch without snapping, essential for securing heavy-duty bales. Bend resistance ensures the wire retains its shape, preventing loosening during transport.
baling wire gauge
Field performance, insights gleaned over time, provide another layer of expertise in selecting the appropriate baling wire gauge. Practitioners often consider factors such as the type of baling equipment used and the average size and weight of the bales produced. Modern balers sometimes require specific wire gauges to function optimally, and adhering to these requirements can enhance bale uniformity and integrity.
Safety should not be an oversight but a core consideration in wire gauge selection. Using incorrect gauges can lead to dangerous failures, resulting in accidents and injuries. Proper training in handling and applying baling wire effectively mitigates such risks, promoting a safer working environment.
Reflecting on these guidelines, it’s evident that choosing the right baling wire gauge is an elaborate process that goes beyond the wire’s physical attributes. It encompasses an understanding of material compatibility, environmental factors, economic balance, mechanical properties, field experience, and safety considerations. This holistic approach provides a foundation for making informed decisions that enhance performance, ensure safety, and optimize costs.
In this exploration of baling wire gauge, it's clear that achieving the perfect balance requires a synthesis of theoretical knowledge and practical experience. Professionals in the field are encouraged to continually assess and refine their gauge selection strategies. With advancements in wire technology and baling machinery, staying informed about industry trends and innovations is crucial.
Overall, effectively implementing the right baling wire gauge can lead to significant improvements in operational efficiency, material conservation, and economic savings, demonstrating the profound impact that such technical details can hold within industrial processes. As an authoritative aspect of the baling industry, mastering wire gauge selection will continue to be a cornerstone of industry best practices, ensuring commercial success and reliability.