Cardboard bale wire may not be the flashiest product in the industrial sector, but it is an indispensable tool that plays a pivotal role in waste management and recycling processes. Its efficiency and reliability in securing bales of cardboard translate into significant operational benefits, and understanding its applications can lead to improved sustainability practices for businesses worldwide.
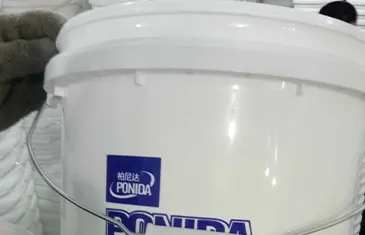
Cardboard bale wire is meticulously designed to provide the strength and flexibility required to secure compacted cardboard effectively. Among the many types of bale wire, annealed and high-tensile wires are the most commonly used. Annealed wires, known for their pliability, are perfect for automatic balers, providing just enough flexibility for the wire to twist and secure without breaking, even under substantial pressure. On the other hand, high-tensile wires are appreciated for their strength in semi-automatic and manual baling operations, ensuring that even the densest bales remain intact.
The expertise surrounding cardboard bale wire isn't just about the material; it's also about understanding the specific requirements of baling machines. Different balers demand different wire gauges; choosing the wrong gauge can lead to inefficiencies, possibly causing machine malfunctions or even operational downtime. For instance, lighter gauge wire might suffice for smaller bales produced by a vertical baler, while horizontal balers that process larger volumes might require a thicker gauge wire to handle the additional weight and pressure.
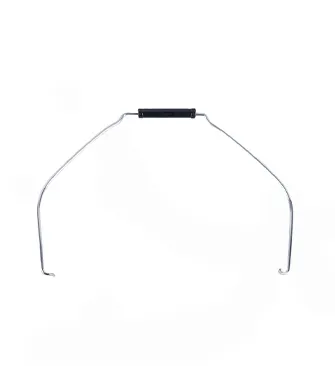
From an authoritative standpoint, manufacturers of cardboard bale wire rigorously test their products to comply with industry regulations and standards. ISO certifications and compliance with environmental standards ensure that the wire is both safe for operational use and environmentally friendly. Additionally, suppliers often offer consultation services, helping implementers select the appropriate type of wire for their operations—promoting both safety and efficiency.
cardboard bale wire
In practice, those who have adopted cardboard bale wire attest to its transformative impact on recycling operations. Facilities that have optimized their baling wire selection process report fewer machine jams and decreased labor costs due to reduced need for manual interference. Furthermore, a well-secured bale means reduced risk during transportation, with less likelihood of bales breaking open and causing safety hazards or product loss.
Trustworthiness in cardboard bale wire comes from seasoned suppliers known for their consistency in quality and service. These suppliers not only provide the wire but also offer insights into best practices for storage and handling to ensure longevity and performance. Preventing rust and deterioration is paramount; therefore, understanding storage conditions—such as avoiding extreme temperatures and humidity—can extend the life of the wire significantly.
Adopted widely in the logistics, retail, and manufacturing sectors, cardboard bale wire has proven its worth through decades of consistent application. Businesses prioritizing sustainability find it indispensable for maintaining efficient recycling practices, reducing landfill waste, and supporting the circular economy. By choosing the right cardboard bale wire, companies demonstrate a commitment not only to operational excellence but also to environmental stewardship.
In conclusion, the nuanced choice of cardboard bale wire impacts not only the efficiency of waste management processes but also operational costs and environmental strategies. Its role may be understated, but for industry insiders, the advantages are clear and compelling. For businesses aiming to optimize their recycling processes, reduce costs, and adhere to sustainability goals, investing in high-quality cardboard bale wire is a decision that promises significant returns.