The meticulous world of rebar tie wire is one that commands attention, both for its indispensable role in construction and the precision required in its application. Rebar tie wire isn't just a tool—it's an essential bridge between raw material and robust infrastructure, ensuring that structures stand solid against nature's whims and the test of time.
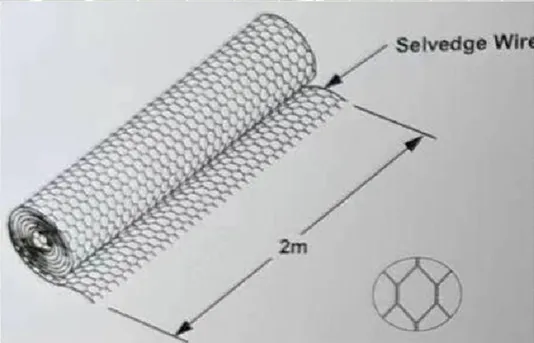
A day on a construction site reveals the critical nature of rebar tie wire, as it weaves through steel reinforcements like an intricate tapestry. Its very presence guarantees the integrity of concrete structures, spanning everything from towering skyscrapers to sprawling bridges. Though overlooked by the untrained eye, this thin yet durable material supports incredible weight and stress, reflecting a profound symbiosis between human engineering and elemental physics.
Diving deeper into the specifics, rebar tie wire typically comes in varied gauges, each serving a particular purpose based on tensile strength and flexibility requirements. Many seasoned experts emphasize the importance of choosing the right gauge, as it directly impacts the durability of the connection. A miscalculation, however slight, can result in a compromised structure, illustrating why mastery in this field cannot be overstated. Professionals in the trade often stand by the saying, Stronger is safer, when selecting their tie wire, ensuring the utmost safety and longevity.
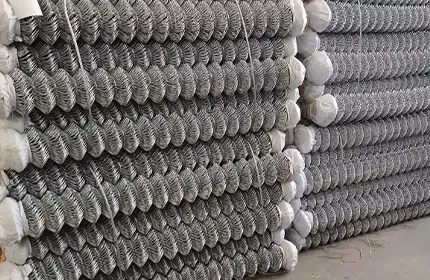
The application process demands dexterity and skill, much like a craftsman honing his art. Workers deftly maneuver the wire around rebar connections,
creating knots that must withstand immense pressure. This task, while appearing simple, requires an acute understanding of tension and physics. Each knot, whether a simple tie or a complex series of twists, is crafted with precision to ensure stability. Missteps are not an option when human lives and investments hang in the balance.
rebar tie wire
Trust in the quality of rebar tie wire is paramount and leads professionals to scrutinize every aspect, from material composition to manufacturing standards. The market offers various options, from electro-galvanized to black annealed wire, each with distinct characteristics suited to specific environmental conditions. Electro-galvanized tie wires, for example, possess rust-resistant properties ideal for structures exposed to the elements, reinforcing the trust professionals place in product specifications and adherence to stringent industry standards.
The continuous evolution of rebar tie wire technology demonstrates the field's commitment to excellence. Innovations such as automated tying tools not only expedite the tying process but bolster precision and consistency, providing a technological edge that translates into practical benefits on the ground. By reducing the time and physical effort required per operation, these advancements help in minimizing fatigue and human error, fostering greater trust in the safety and reliability of modern construction techniques.
In conclusion, while rebar tie wire might be a humble component in the colossal enterprise of building, its impact is anything but insignificant. It demands respect and the keen eye of a seasoned professional who understands that the world rests quite literally on their shoulders. The real-world experiences of professionals underpin the expertise, trustworthiness, and authority that define the rebar tie wire industry, ensuring that structures not only reach for the sky but also stand firm against the eons.