Mastering the Technique An Expert Guide to Tying Metal Wire for Industrial Applications
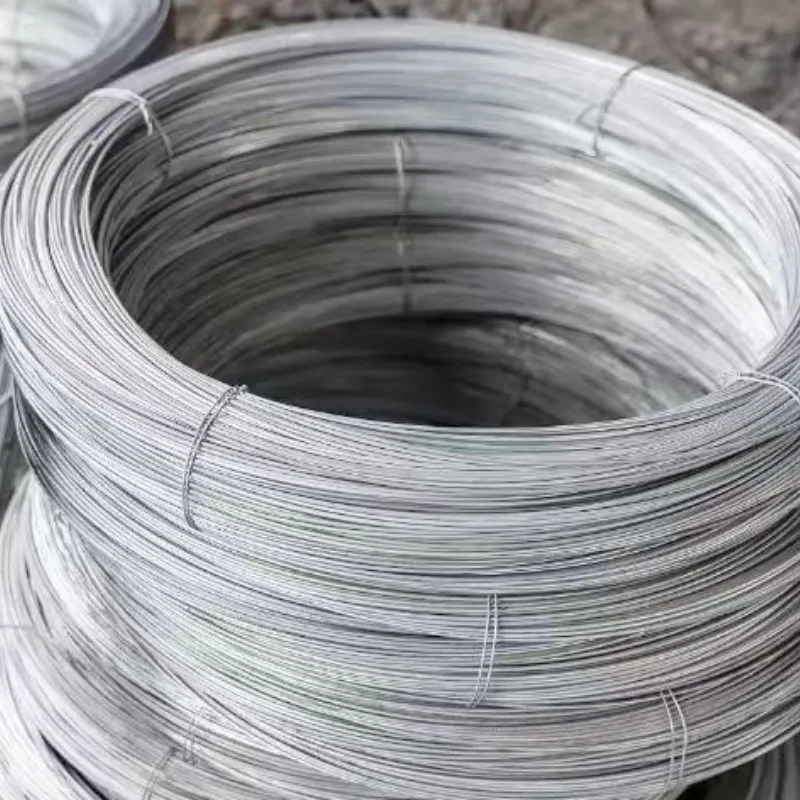
In the realm of industrial manufacturing, the seemingly simple task of tying metal wire holds significant importance. Whether it's for securing materials on a construction site, bundling automotive components, or ensuring art installations withstand the test of time, mastering this technique is crucial. The finesse involved in tying metal wire extends beyond mere utility; it requires a nuanced understanding of materials, techniques, and industry standards.
Experience plays a pivotal role in perfecting the art of metal wire tying. Industry veterans often recall their early days of grappling with unwieldy wires, learning gradually through trial and error. The tactile feedback from the wire, the tension in the hands, and the sound of the wire as it's manipulated all contribute to a comprehensive sensory experience. These elements converge to refine one's skill over time, allowing seasoned professionals to execute precise and enduring ties swiftly.
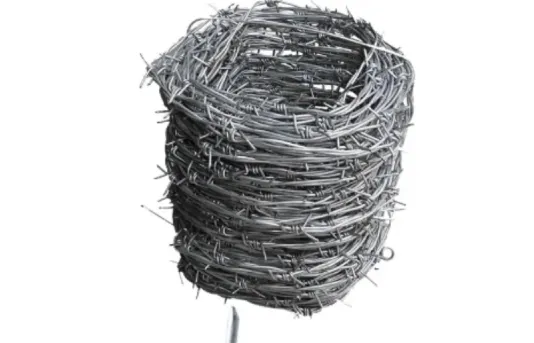
Professional expertise in this area is not just about handling the metal. It starts with understanding the types of wire available. Galvanized steel, copper, aluminum, and stainless steel are popular choices, each offering distinct advantages. For instance, galvanized steel wire is celebrated for its corrosion resistance and tensile strength, making it suitable for outdoor applications. Understanding these properties aids in selecting the appropriate wire type for specific needs, ensuring functionality and longevity.
Once the type of wire is chosen, the technique of tying it becomes paramount. The basic knot, often a simple twist, is just the beginning. Complex bindings such as the double loop knot, figure-eight knot, or the clove hitch provide additional security. Mastering these knots requires patience and practice, as each knot applies different amounts of stress and strain to the wire, influencing its performance under load. Advanced techniques also include using tools like pliers or wire-twisting machines to achieve tighter, more secure ties.
tie metal wire
Authoritativeness in the field of metal wire tying is established through adherence to industry standards and continuous innovation. Numerous organizations, such as the American Society for Testing and Materials (ASTM), offer guidelines and standards for wire usage in various industries. Familiarity with these guidelines ensures compliance with safety and quality requirements, an essential factor in maintaining credibility and trust in industrial practices.
Furthermore, manufacturers and engineers who innovate new applications and improvements in wire tying technology contribute to advancing the field. Keeping abreast of the latest innovations, such as biodegradable wire options or enhanced coating methods, further establishes one's authority.
Trustworthiness, in this context, is garnered not just by performing a task effectively but by ensuring durability and safety. The repercussions of poorly tied metal wire can be severe, ranging from financial losses to safety hazards. To mitigate these risks, regular training sessions, certifications, and inspections are vital. By adopting a culture that prioritizes skill enhancement and safety compliance, professionals demonstrate their commitment to maintaining high standards and trustworthiness in their work.
In conclusion, tying metal wire is a critical skill encompassing experience, expertise, authoritativeness, and trustworthiness. It's an art and science, requiring a balance of hands-on practice, technical knowledge, adherence to standards, and commitment to safety. For those in the industrial sector, mastering this technique not only improves efficiency but also underscores a dedication to quality and innovation, ensuring that projects are completed with precision and care.